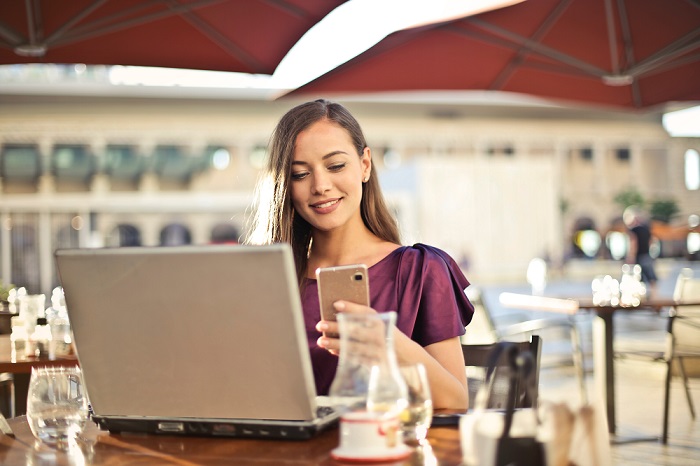
BCS WIP & ROUTINGS
BCS’s Routings and WIP abilities when enabled allows organizations to define proper routing for their manufacturing process including the resources required to finish the process, along with the cost required and expected time. Basis is also provided by Routings for infinite engine capacity scheduling to help find out the resources that are under-utilized or exhausted. Finally, capturing consumed materials’ cost during manufacturing process helps generate clear image of the procedure expenses prior to finalizing and commitment to GL.
Key Functionality
Track Work-in-Progress expenses
Drag & Drop GANTT style scheduler
Infinite ability scheduling
Accurate costing
Work center management
Process Flow
Assembly Item
A manufactured item in BCS, consuming other components as a process part is termed as Assembly item. It is defined easily via New Items menu. Optionally, assembly items can be related to several numbers or serialized. Choosing any of the options is likely to ensure stringent maintenance of full traceability for required products.
Location settings
BCS has one interesting unique feature, which is setting up of the system to manufacture same product, but in different types to every location. It is possible to assign routing and work in process to individual location level. For instance, Light assembly process can be performed and materials backflushed in one location. However, collect labor costs and define routine at another.
Manufacturing cost templates
It defines all indirect and direct costs related to the operation’s routing, combined with accounts, where posting of such costs is done to. On completion of operation each time, associated cost template is used by BCS to offer baseline form to product costing and still maintain flexibility.
Work Center Management
Prior to defining manufacturing procedure using routings, setting up work centers used by the routing is essential. Every work center might represent a person, machine, department or work cell, involved with the manufacturing procedure. This work center list can be termed to be an integral part of real-time scheduling engine.
Production Routing
After defining cost templates and work center, production routings can be established to represent each step undergone by the product, the anticipated run and setup times, associated work centers and cost templates to be used. It facilitates real-time scheduling procedure, defaulted to backward or forward and over-ridded on case to case basis.
Work Order
Generating Work Order in BCS actually is regarded to be an optional step during the manufacturing process. But, if capability is desired by the business to come up with a schedule and make clear communication with the production n what requires to be created, when and the components that are to be used, or if a configurable product is sold where options and features are present, then it is a critical part to generate work order, considered to be a crucial part and also termed to be the initial point to implement production control system.
Dispatch List/ Work Order Traveler
Work Order Traveler can be stated to be a printable document which is handed to the production department to communicate effectively the routing steps, schedule and production plan. It also communications the amount of time consumed by each operation including the raw material amount consumed compared to expectations.
But Dispatch List offers detailed material list necessary for work order.
Inventory Commitment
BCS’s capability to commit automatically inventory to production is activated with the generation of Work Order, so as to offer real-time and accurate inventory status report.
Work Order Management
Statuses are included to Work Order with Routings and WIP, thereby allowing more finite control level as to how and when work orders get released to production including clearer visibility with regards to production status.
Released
Open Planned
Firm Planned
In-Process
Closed
Complete
There are available mass update screens to allow production managers to make huge changes and be on top of statuses, based upon variety of criteria, like due dates, item and customer. Such statuses are also updated using workflow engine to allow more automated procedure.
WIP Issue
Such transaction issues materials manually to WIP and Work Order and are consumed. Fr manufacturing products taking longer time to complete as well as having numerous work orders open through the work end find it quite valuable.
Work Order Completion
Numerous purposes are served by completion transaction:
Reporting of completed products
Recording scrap
Issuance of materials
Recording labor vs. operation
Work Orders comes with 2 step closing procedure with BCS. The first step however, is completion, which is performed typically by someone responsible with production. It also indicates actual time of completion of a product and its availability in the inventory.
Work Order Close
It is considered to be the procedure’s second phase allowing finance, production and cost accounting team to come together to preview the expenditure applied to every Work Order prior to commitment of GL expenditure.
ENJOY ALL THE POS FEATURES
DOWNLOAD 30 DAYS FREE TRIAL !
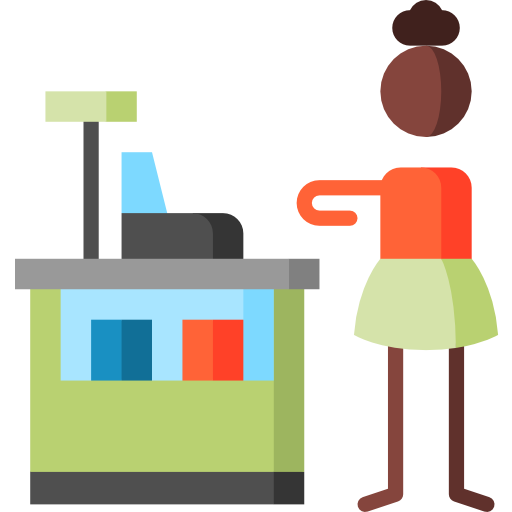